Surface treatments
Surface treatment is where it all started for us, and we’re still unashamedly good at it. Surface treatments are used to give products different technical, mechanical and visual characteristics. Coatings can be used to influence the technological properties, durability and service life of a product or piece. In addition, the surface treatment affects the electrical conductivity of the product.
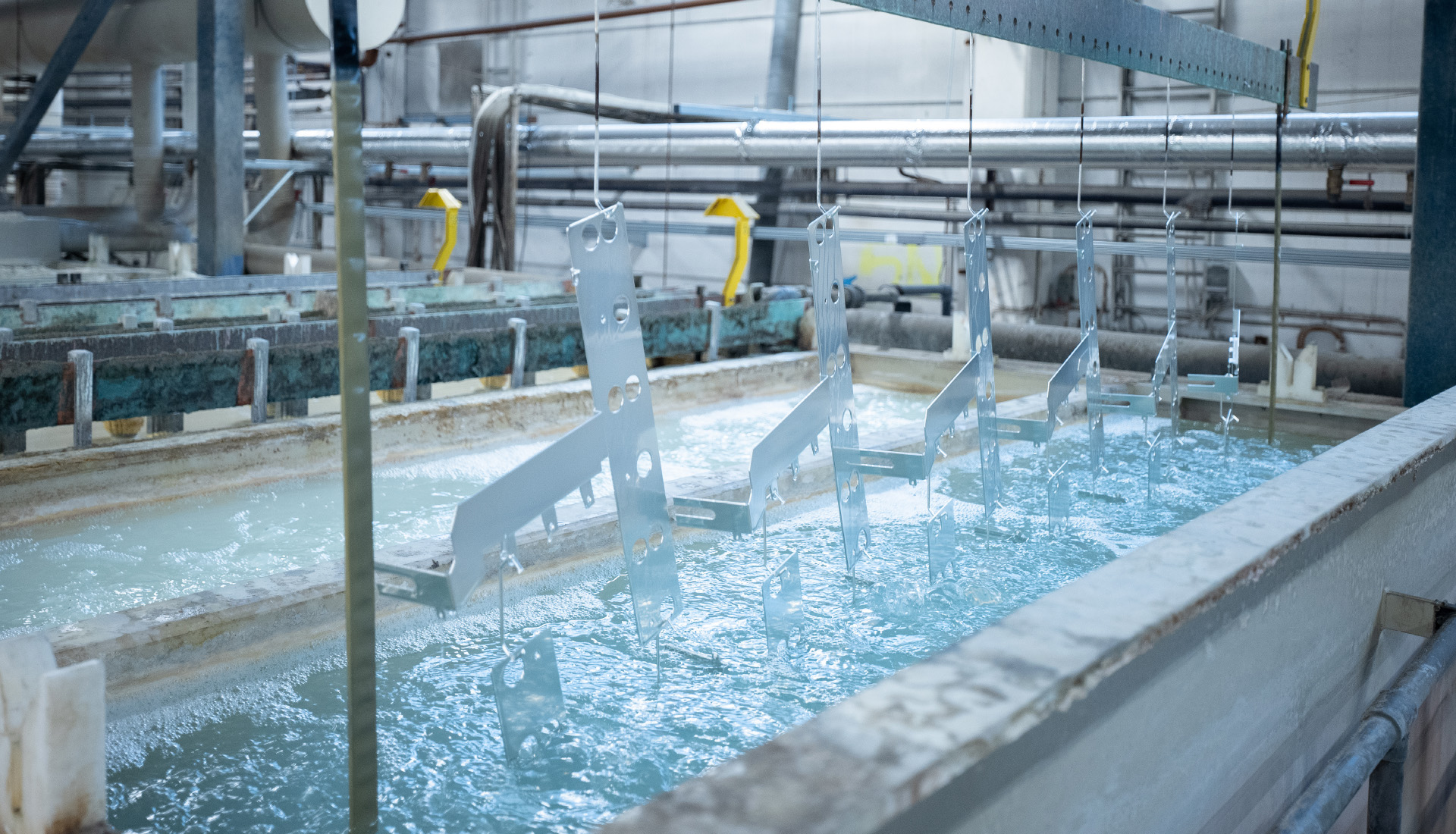
Along the way, we have found that the more comprehensively the entire manufacturing process is managed in one place, the more certain the end result: we can influence the quality of the final product with the best and most suitable surface treatment processes, and we can ensure that the same product is manufactured using only those materials and processing methods that bring out the best in the coatings.
Our versatile surface treatment lines allow us to choose the coating line and process that best suits the product in terms of size, shape and material. We specialise in the surface treatment of components used in electrical equipment, for which we offer both individual coatings and combinations of coatings.
We are able to surface treat products of many sizes, from small turned parts to large three-dimensional pieces or products measuring 3000 x 1100 x 500 mm.
Electrolytic surface treatments
Electrolytic surface treatment processes give products, among other things, a long service life and mechanical resistance, while providing highly electrically conductive surfaces. At Laitila, we carry out surface treatments with tin, silver, nickel, nickel-tinall and nickel-chromium, as well as chrome-free passivation for aluminium alloys.
For telecommunication connectors with low voltage and current values, we recommend nickel or silver plating, which conduct electricity very well. We are able to perform electrolytic surface treatment both in drum and hanging. Drum plating is best suited for small product sizes, typically e.g. turned components and larger products are best handled by hanging.
Careful quality and process control is carried out, including surface thickness measurement, e.g. by X-ray equipment. We also regularly test, among other things, the adhesive strength and carry out various process analyses, for example to measure chemical and metal concentrations.

Powder coating
Powder coating gives products good corrosion protection. It is well suited for the coating of various sheet metal parts. The pre-treatment of the product to be coated is particularly important for the success of powder coating.
After the washing processes, the parts are treated with different activators and corresponding processes. Epoxy, polyester or mixed powders are then sprayed onto the surface of the piece using static electricity. After spraying, the powder is “baked” in a furnace, forming a smooth and beautiful visual protection on the surface of the piece.
The best results are achieved when the materials, substances, chemicals and processing methods used in manufacturing and pre-treatment are considered at the prototyping stage to ensure that they are seamlessly compatible with the surface treatment.
We paint simple pieces on an automatic line, but for complex products, such as case-shaped and other demanding items, we can also complete and paint manually. As a completely new surface treatment, we offer electrical insulation powder coating, which can replace the challenging process of post-processing and installing insulating socks on power rails, for example.